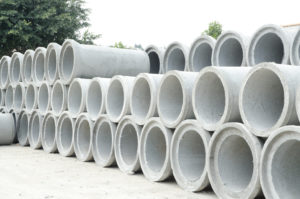
Concrete in certain environments is subject to sulfate attack. These include seawater, some industrial environments, sanitary sewers, and sulfate-bearing soils and groundwater. As engineers have known since the early 1900s, the latter commonly occur in the western United States and the prairie provinces of Canada, as well as in other parts of the world. Some aggregates contain gypsum, which can be a source of internal sulfate attack.
Mechanisms of sulfate attack
Whatever their source, sulfate ions react with the hydration products of portland cement. The key component in the reaction is the hydration product of tricalcium aluminate, or C3A in cement chemistry notation. C3A hydrates to form monosulfate. Cement contains some sulfates to control setting. They react with the monosulfate to form ettringite before the concrete sets.
After the concrete sets, additional sulfates are problematic. Ettringite formation is an expansive reaction which causes cracking in hardened cement paste.
Ettringite deposits in concrete are not always a sign of either sulfate attack or delayed ettringite formation. Cycles of wetting and drying may allow ettringite that was already present to dissolve and then redeposit in voids. Such deposits are harmless; they do not “clog” air voids or render them incapable of protecting the concrete from freeze-thaw damage.
Once all the monosulfate is gone, the sulfates react with calcium ions and water to form gypsum. This, too, is an expansive reaction that causes cracking.
That’s not the only problem, though. Forming ettringite from monosulfate takes more calcium, which has to come from somewhere. Normally the source will be calcium hydroxide, which is highly soluble. Depletion of calcium hydroxide leaves the concrete more porous and permeable. Sulfate attack also destabilizes the calcium silicate hydrate, resulting in softening and loss of cohesion.
In the field, sulfate attack manifests itself in loss of strength, expansion, spalling of surface layers, and ultimately disintegration.
Not all sulfates are equal
Sulfates don’t exist on their own. Depending on which cation they are associated with, they can be more or less aggressive. The least aggressive is calcium sulfate (CaSO4) because it’s the least soluble. And because it supplies calcium for the reactions, it doesn’t attack the calcium hydroxide. Even so, it will cause expansion and cracking due to ettringite formation.
Sodium sulfate, Na2SO4, is moderately aggressive. Because of the sodium ions, there’s plenty of NaOH in solution to maintain the stability of the calcium silicate hydrate gel, the main strength-producing component of the cement paste. Unlike CaSO4, though, it doesn’t supply calcium, so it will attack the calcium hydroxide. It causes expansion and cracking due to the formation of both ettringite and gypsum.
Magnesium sulfate, MgSO4, is the most aggressive. The presence of poorly soluble Mg(OH)2 destabilizes the calcium silicate hydrate gel. In addition, MgSO4 transforms calcium silicate hydrate gel into ettringite. This causes softening and loss of cohesion of the cement matrix.
Sulfate-resistant concrete: the chemistry
In sum, sulfate attacks calcium hydroxide, calcium silicate hydrate, and the products of C3A hydration. If we want to make sulfate-resistant concrete, it makes sense to minimize the vulnerable components. Indeed, reducing the C3A content is how we make Type V (sulfate-resistant) cement.
Calcium hydroxide is a product of the hydration of the calcium silicates in cement. They give us the main strength-producing component in cement paste, so we don’t want to eliminate them. But we can incorporate supplementary cementitious materials into the concrete. They react with the calcium hydroxide to form more calcium silicate hydrate, filling some of the voids. That is, we replace a weak, soluble material with a stronger material and make the concrete less permeable.
Type V cement is not available everywhere, but we can obtain equal or better performance with supplementary cementitious materials. However, some supplementary cementitious materials contain reactive alumina, so it’s important to select the right ones and get the proportions right. You can test a cement or combination of cementitious materials for sulfate resistance using ASTM C1012.
Sulfate-resistant concrete: the physics
An appropriate water-cementitious materials ratio is essential. The less permeable the concrete, the longer it takes for the sulfates to penetrate it. If you want your concrete to perform well, you need to ensure not only the appropriate ingredients and mixture proportions, but also good craftsmanship. In this case, a long, moist cure is especially important because most supplementary cementitious materials hydrate slowly. Low permeability is even more important than cement composition when it comes to resisting sulfate attack.
Of course, it makes no sense to have a low-permeability concrete between the cracks. We’ve discussed minimizing thermal cracking and shrinkage cracking in previous blogs.
Evaluating the exposure conditions
For sulfate exposure, ACI 318 defines four exposure classes in terms of both water-soluble sulfate in soil and dissolved sulfate in water. To determine the severity of sulfate exposure of a specific environment, analyze the soil in accordance with ASTM C1580.
It’s important to note that some environments constitute more than one kind of exposure. For example, seawater contains both sulfates and chlorides, and you need to design for both. However, the chlorides mitigate the expansions that would normally occur with sulfate attack. So the corrosion exposure class is C3 (the most severe), but the sulfate exposure is only S1. Because of this, limiting the C3A content of the cement is not appropriate. While C3A is not good in a sulfate environment, it is extremely helpful in a corrosive one. That’s because the products of C3A hydration adsorb chlorides, keeping them from penetrating deeper into the concrete. Slag cement also adsorbs chlorides, so it’s an excellent choice for concrete in a marine environment.
Sadly, there’s no such thing as sulfate-proof portland cement concrete. Particularly when the sulfates occur as MgSO4, it’s just a matter of time before the concrete disintegrates. In very severe sulfate exposures it may make sense to install a protective barrier for the concrete. For example, you may want a liner in a sanitary sewer pipe.
Internal sulfate attack
As mentioned above, aggregates may contain sulfates, either as an original component or due to oxidation of sulfides originally present. Either way, these usually occur in the form of gypsum. It may be a coating on sand or gravel, a component of sedimentary rock, or in weathered slags. Gypsum-bearing aggregates occur throughout the Middle East. Aggregates made from recycled building materials may be contaminated with gypsum from wallboard.
If the gypsum occurs primarily within a particular size fraction, it is best to remove that entire fraction from the aggregate. No concrete will withstand internal sulfate attack from gypsum-bearing aggregate in the long term.