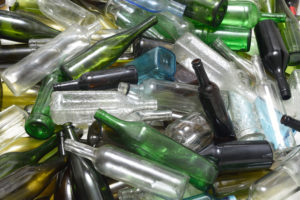
We’ve previously discussed a new standard that promotes sustainability through the use of ground recycled glass in concrete. Now let’s get some background on ASTM C1866.*
Most glass falls into one of three categories:
- Container glass in bottles and jars is usually soda-lime glass. It comes in clear, green, amber, and blue.
- Plate glass for glazing in buildings and cars is also soda-lime glass. It may be clear or tinted.
- E-glass for fiber-reinforced polymers is low-alkali glass.
Manufacture of all three types requires careful control, so the chemistry is very uniform worldwide. That uniformity, as well as the abundant supply, makes it a good potential resource for use in concrete.
We often add supplementary cementitious materials—that is, fly ash, slag cement, or silica fume—to concrete. These materials react with calcium hydroxide, a product of cement hydration, to form calcium silicate hydrate. This is the pozzolanic reaction. Calcium hydroxide is weak and water-soluble, which makes it undesirable in concrete. On the other hand, calcium silicate hydrate is strong and insoluble in water. In addition, it takes up more space than the calcium hydroxide it’s made from. That is, the pozzolanic reaction fills up pores, making the concrete less permeable. So the pozzolanic reaction promotes durability as well as strength.
As we seek to produce less greenhouse gas, we’re closing coal-fired power plants. Burning coal is the source of fly ash, so we’re starting to experience shortages of good fly ash. One way to deal with that is to use a marginal fly ash, following the protocols in ASTM C1709. However, in the case of ground glass, ASTM C1866 makes it a lot easier to use the material with confidence because we already know a lot about how it behaves.
Background on ASTM C1866: ground glass as pozzolan
What makes a good pozzolan? Reactive silica—that is, SiO2 that’s glassy and/or fine enough to react readily. So all we have to do with glass is grind it finely enough.
There is a twist, though, with the soda-lime glass in bottles and plate glass, because of its high alkali (Na2Oeq) content. As we discussed previously, some aggregates are subject to alkali-silica reaction. With glass from bottles or windows, we need to make sure it’s not going to be a problem with reactive aggregates. That’s why ASTM C1866 has provisions for using high-alkali container- and plate glass as a means of mitigating alkali-silica reaction. Researchers have found that high-alkali ground glass does mitigate expansions due to highly reactive aggregates, but is not sufficient by itself. However, ternary combinations using other supplementary cementitious materials do give good results.
Another reason we use pozzolans in concrete is to increase its ability to resist the ingress of chloride ions, which promote the corrosion of reinforcement. Here, ground glass performs very well. In tests using either just ground glass or ground glass with other supplementary cementitious materials, ground glass dramatically reduced the total charge passed using ASTM C1202. That is, if you need to reduce the charge passed to less than 1000 coulombs you can do it with ground glass, with or without another supplementary cementitious material.
Lastly, research shows that ground glass can improve the resistance of portland-cement concrete to sulfate attack. That matters in the western United States and Canada, where sulfate soils are prevalent, and in sanitary sewers.
*Kaminsky, Amanda; Krstic, Marija; Rangaraju, Prasad; Tagnit-Hamou, Arezki; and Thomas, Michael D.A. “Ground-Glass Pozzolan for Use in Concrete,” Concrete International, Vol. 42, No. 11, November 2020, pp. 24-32.